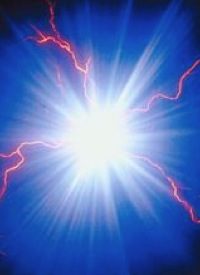
To provide our personal transportation for the foreseeable future, the United States needs oil or an oil substitute.
Electric vehicles, the proposed solution by many for America’s transportation problems, have serious drawbacks generally ignored by a pliant news media. Besides being automotive weenies, their batteries don’t hold a sufficient charge for many everyday trips, and require hours to recharge — unless you want to charge them quickly (thus shortening their life span) and pay the $3,000-5,000 price for replacement batteries. One might also ask: “Where is the electricity to come from if electric cars become ubiquitous?” It is estimated that it would require a dozen 1,000-megawatt power plants to replace the petroleum fuels in Los Angeles alone.
The “hydrogen economy” is a total farce. Hydrogen-powered cars are about as practical as licorice submarines.* Their only reason for being is to prove to a naïve public that the manufacturer is in on being “Green.” No, we need oil or something like it for the foreseeable future.
President Bush, with the backing of many Republicans and most Democrats, claimed to answer this need by requiring the use of billions of gallons of ethanol and biodiesel. Made by a laborious distillation process from corn and soybeans, they are on the market solely owing to mandates and subsidies. In fact, because making ethanol is so energy intensive, debates are still ongoing over whether ethanol creates more energy when it is burned than is used in its creation. Of course, burning our food supply is proving (as we, and most everyone who knew anything about the topic, predicted)† not to be a solution either. While any positive energy output from ethanol production is still hotly debated, the resultant higher prices and food shortages are not in question, as evidenced by the “tortilla riots” in Mexico over the past year.
Another Ethanol?
Having been burnt by the ethanol fiasco, which has caused great misallocations of resources that will come to haunt farmers and entrepreneurs who have invested in ethanol plants, one tends to be cautious when another bioscheme becomes the rage. And algae production is fast becoming just such a rage. There are, however, major differences.
- Algae can thrive in fresh, brackish, or seawater — and very little of that is required.
- There is no need for any soil, much less good soil, as algae grow hydroponically.
- With more than 20,000 known varieties of algae, species can be chosen for high lipid content (e.g., for diesel fuel) or high sugar content for distillation purposes.
- In desert climes it can be harvested on a day-by-day basis because it grows so quickly.
All it takes is sunlight, water, and carbon dioxide to provide the energy for arguably the most complex process we see in nature: photosynthesis.
Here Comes Da Sun
In its most elementary depiction, photosynthesis is a process where light energy converts carbon dioxide and water into oxygen and carbohydrates such as sugars, starches, and cellulose. It, in effect, converts the electromagnetic energy of sunlight into chemical energy that can be used as food to sustain the animal world, or as a fuel such as wood to provide warmth or for other energy requirements.
Nature isn’t in a big hurry to carry out this process, nor is she particularly worried about efficiency. As Howard Hayden points out in his very readable and informative book The Solar Fraud, New England forests convert only about 0.06 percent of the incident solar energy into chemical energy. Corn fares a bit better. Iowa, with an average insolation (the rate at which the sun’s radiation strikes a surface) of 170 watts per square meter, produces about 150 bushels of corn per acre per year, with an energy content of 404 megajoules (MJ) per bushel if you burn the corn directly as fuel. (Gasoline, by comparison, has approximately 121 MJ per gallon.) This works out to a sun-to-corn efficiency of 0.28 percent — unless you make ethanol out of it. Then you only convert 0.14 percent of the incoming solar energy to usable chemical energy.
Fortunately, the soft-energy folks are right in thinking that there is a lot of solar energy beating down on planet Earth, else there would be precious little plant or animal life. In Albuquerque where the average insolation is 240 watts per square meter, the equivalent of the energy in 254,000 gallons of gasoline falls on each acre over a year’s time. Yes, there’s plenty of sunlight; utilizing it economically is the problem.
It seems obvious that a major problem in obtaining chemical energy from plants is raising the percentage of solar energy that is converted to a form we can use for something other than working on our tans. Indeed, this is what the proponents of growing algae as a feedstock for biofuels have in mind. The first to develop an efficient and reliable process to grow algae at super-fast rates is likely to win a multi-billion-dollar prize, along with the gratitude of millions of Americans. Let us take a look at the present state of affairs as pertains to the conversion of algae into products that can be used for transportation fuels.
How It Would Work
To create diesel fuel or gasoline from algae, the oils must be extracted from the algae — it is one of the major cost factors in the production of algae-based fuels. Three processes are under consideration:
- Pressing with an “expeller,” a process that can extract 70-75 percent of the oil.
- Use of hexane as a solvent to leach out the oil, which, along with pressing can extract more than 95 percent of the oil; however, there are inherent dangers here due to the volatility of hexane solvent.
- Supercritical fluid extraction — the use of liquefied CO2 under pressure to act as a solvent to extract the oil. Almost all of the oil can be extracted using this process alone, but special equipment is necessary to maintain pressures and temperatures.
Oils from the algae are then “cracked” in a manner similar to petroleum whereby hydrogen is used to break the long hydrocarbon chains, creating what is called “green crude.” The end product is crude oil that is almost chemically indistinguishable from light, sweet crude oil, except that it is green in color.
This green crude does not have the drawbacks of biodiesel, which needs special care in its storage, transport, and use (being no more than high-grade plant or vegetable oil, it solidifies when it gets cold), and ethanol, which, too, cannot be transported using traditional pipelines, along with its numerous other problems.
The production of this product is also carbon neutral — the outcome that is sought for by worried environmentalists in biodiesel and ethanol production. Except for possible carbon dioxide created by the production of hydrogen for the cracking process (depending on what energy source is used in the hydrogen’s production), the carbon dioxide created by burning the products formed from the green crude — gasoline, diesel fuel, jet fuel, methane gas, etc. — cannot be greater than the carbon dioxide yanked by the algae from the atmosphere during photosynthesis.
The main sticking point in creating green crude from algae lies in producing enough high-energy-content algae to feed our country’s energy appetite. Can companies overcome the obstacles? You be the judge.
What Stands in the Way
Growing algae in and of itself is no trick; varieties of it will literally grow in almost any type of brine or even wastewater. However, growing, or culturing, a single, desired alga variety is more difficult. If algae are grown in open ponds, they are susceptible to being killed off by invasive algae and bacteria. In open ponds, fluctuating temperatures and pH levels also can kill off algae. Strains of algae that can fend for themselves in an open pond may not be strains that have optimal energy-producing qualities. Closed growing systems also have their problems: electing and “domesticating” superior species is proving to be difficult, as is introducing enough carbon dioxide (plant food) into the enclosed systems.
Even once the algae are grown, commercially viable amounts of available green crude are not a done deal. None of the proposed processes has undergone the rigors of commercial/industrial production. Economical methods to harvest the algae and extract the lipids or other carbohydrates have not been developed, and factors influencing any resultant fuel quality and properties are not yet well understood.
The obstacles notwithstanding, a survey of the literature indicates that there is a great deal of activity among those who believe the pros outweigh the cons in the development equation. Indeed, one commentator observed that companies are springing up on a near-daily basis, driven by both the ultimate prize and the fact that the capital investment for a start-up company is low as compared to wresting oil from shale formations or converting coal to liquid fuel. Examples of companies active in developing algae-to-fuel technology are noted below.
Solix Biofuels
Using triangular containers termed “photobioreactors” (PBRs), inventor Jim Sears brings together algae, water, carbon dioxide, and sunlight in order to “farm” his crop of biofuel feedstocks. Sears, of Ft. Collins, Colorado, has already learned that this simple formula isn’t quite as simple as it may initially appear. The high-oil-content algae species his company has selected is finicky about water temperature, and the normal amount of CO2 in the atmosphere isn’t sufficient to achieve maximum growth. He thinks algae farms will have to be located near power plants — although the problem of separating CO2 from other stack gases has proven to be a sticky one. At least there shouldn’t be any shortage of CO2, as a 1,000-megawatt coal-fired plant produces 360 pounds of the gas every second.
Solix CEO Doug Henston predicts algae would produce 10,000 gallons of oil per acre, per year. Currently soy produces some 50 gallons of oil per acre; canola, 150 gallons; and palm, 650 gallons. As vegetable oil typically has 94-95 percent the heat content of diesel fuel, 10,000 gallons would produce some 1.4 million MJ of energy per year — a whopping 4.5 percent of the incident solar energy and some 75 times the conversion rate of an oak tree.
Henston reports that his company is still in the development mode and plans a larger research project to be completed late summer 2008, which will tap into the New Belgium Brewing Company as a source of growth-enhancing CO2. Solix is financed by private equity, with $5 million having been raised and plans to raise another $10 million during 2008.
Valcent Products
In his “vertical greenhouse” near El Paso, Texas, plant physiologist and Valcent Products CEO Glen Kertz has developed a unique method of exposing algae to sunlight in order to produce the greatest amount of biomass in the shortest period of time. The device, known as a High Density Vertical Bioreactor (HDVB), or “VertiGro” system, uses a series of transparent horizontal chambers (reactors) connected in series so the algae solution is exposed to sunlight while flowing down after having been pumped up from a reservoir. The process is then repeated. Being a closed-loop system, almost no water is used except that required to feed the algae. Kertz maintains that algae is the fastest-growing plant on Earth, and in some species as much as 50 percent of the “body weight” is vegetable oil (lipids). Moreover, he claims that by selecting the right species of algae, Valcent will be able to tailor the carbon chains for those most effective in producing a menu of transportation products such as diesel or jet fuel.
Kertz is even more enthusiastic than Henston in his estimation of yields: 20,000 gallons of oil from an acre of pond, ostensibly much more from the VertiGro system. He calculates that an area one-tenth the size of New Mexico in algae production would meet the fuel demands for the entire United States.
PetroSun
Scottsdale-based PetroSun, already a player in the oil and natural-gas industries, plans to open a 1,100-acre saltwater open-pond system with 94 five-acre and 63 10-acre ponds. Located on the Texas Gulf coast, it plans to extract oil on-site and then barge or truck the raw oil to a biodiesel refinery.
The company plans additional algae sites and extraction plants in Alabama, Arizona, and Louisiana.
The interest in algae-to-oil is certainly not limited to the United States. Prototype production is underway in Israel and New Zealand, with the aforementioned PetroSun planning facilities in Mexico, Brazil, and Australia. At this point in time all of these plants have one thing in common: they are not yet producing any fuel. It may well come to pass — and there is certainly “a lot of attempting going on out there” — but the process may well prove to be more difficult than it seems to be at first glance.
One very encouraging sign, however, is the lack of interest the federal government is showing in algae-to-oil production. The energy legislation of the federal government — particularly with Democrats in control of the House and Senate — is focused on those technologies that don’t have a chance of producing significant energy. The politicians are buying off special-interest groups that can’t legitimately compete in the energy market. In light of this, it may well be that algae could play a key role in our energy future.
* See the author’s article “The ‘Hydrogen’ Economy,” available online at www.thenewamerican.com.
† See the author’s article “Going Bananas Over Ethanol,” available online at www.thenewamerican.com.