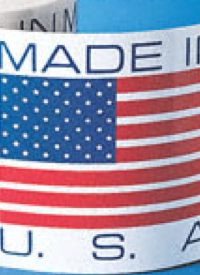
The press release from the Boston Consulting Group signaled the beginning of the American renaissance in manufacturing as cost advantages of China are fading rapidly and companies are beginning to repatriate their jobs back home. There are seven industrial sectors that could create two to three million jobs over the next five years as American manufacturers do the new math. As explained by Harold Sirkin, one of the three authors of Made in American, Again: "A surprising amount of work that rushed to China over the past decade could soon start to come back — and the economic impact could be significant. We’re on record predicting a U.S. manufacturing renaissance starting by around 2015."
The seven industry groups which could enjoy the most significant benefits are transportation goods, electrical equipment and appliances, furniture, plastics, rubber products, machinery, and computers. The resultant sea-change by repatriating jobs in these industries would be massive, potentially adding $100 billion to America’s GDP, while reducing oil consumption due to lower transportation costs.
China is facing severe head winds in its fight to stay competitive. Wages have been rising there by 15 to 20 percent a year, while the value of the dollar continues to decline against the yuan — which effectively has increased costs of doing business in China by 23 percent over the past five years. The advantages of bringing jobs back to America are already showing up in the import numbers. From 2001 through 2004, imports from China grew by about 20 percent a year. But those imports have dropped to just four percent in the past couple of years.
Companies already enjoying the shift in dynamics include Ford, NCR, All-Clad Metalcrafters (a high-end cookware maker), Peerless Industries (an audio-visual equipment manufacturer), Chesapeake Bay Candle, and ET Water Systems (a maker of irrigation controls). And it’s not just about the closing of the gap between wages in the two countries. The lead time between orders and receipt of goods is typically three weeks and sometimes as long as nine months. And U.S. manufacturers also have issues related to Chinese subcontractors' sluggish response to design changes.
Ford is bringing up to 2,000 jobs back to the United States now that it has successfully negotiated a two-tier salary program with the unions, allowing the company to hire new workers at just $14 an hour. Peerless is consolidating all of its manufacturing facilities in Illinois, resulting in significant cost savings, shorter lead times, and local control over the manufacturing process. Outdoor Greatroom Company (maker of fire pits and outdoor shelters) moved jobs back to the United States partly because it took Chinese contractors up to nine months to complete orders.
Current assumptions about the state of American manufacturing are also turning out to be inaccurate. According to the Boston Consulting Group, the domestic industrial output of the United States is nearly two-and-a-half times its 1972 level (adjusted for inflation), despite employment having dropped by one-third. And from 1997 to 2008, U.S. manufacturing output increased by one-third to $1.65 trillion. With wages that have remained level or even declining, the weaker dollar (which makes American exports appear cheaper to foreign consumers), an increasingly flexible workforce, and skill sets that equal the best in the world, the advantages of keeping jobs at home continue to increase.
In a revealing interview in the New York Times, Taphandles founder and president of the beer-marketing products company, Paul Fichter, noted that he had just signed a lease on a 41,800-square-foot factory in Woodinville, Washington, where he expects to hire 150 workers to make signs and displays such as A-frame chalkboards seen outside bars, taverns, and restaurants:
Q: Why did you decide to open your new factory in the United States?
A: The lead time for orders coming from China is three weeks, and all of our brewery clients want our products faster…
Q: Were there other factors?
A: Our Chinese labor costs have increased 300 percent since 2006 when we opened our factory there. Even at the higher wages Chinese workers are demanding, it’s gotten harder to find labor. To stay competitive we’ve also had to upgrade benefits like dormitories and food. On top of that, the Chinese currency continues to appreciate … and I predict that shipping costs will keep going up as a result of the rising cost of oil.
Q: What type of workforce will you need?
A: Mostly skilled technicians … the cost of computer automation in the United States has also dropped. In China, humans do the same work on much simpler machines. So we’re replacing Chinese labor with machines run by United States workers. The machines will make 10 times more product than a person could in China.
Q: Do you think Americans still know how to make stuff?
A: Absolutely. The key to success for the United States will be using machines instead of brawn. While I’m really proud of creating jobs here in America, it’s not just an emotional decision. It makes sense.
The renaissance of American manufacturing has already begun. It’s remarkable how the free market, when left alone so that entrepreneurs such as Fichter can make intelligent, profitable decisions, will inevitably adjust imbalances and provide new opportunities.
It’s a lesson that will become increasingly obvious as the shift back to America gains momentum.