At first glance the concepts of horizontal drilling for oil and natural gas and hydraulic fracturing, a method of extracting oil and gas from tight shale formations, seem physically impossible. But tens of thousands of gas wells already using this revolutionary technology prove otherwise. Hydraulic fracturing of underground wells is not a new idea, having been used for about a century to increase flow in water wells. When formations are “tight” or clogged, reversing the flow temporarily with high pressure from inside the well often allows more flow. But there, the similarity with today’s technology ends.
Known as “fracing” (pronounced FR?K-ing), the process begins with a large diameter hole (about 20 inches) drilled and cased to a depth of 18 to 20 feet. This “cellar” keeps the bore hole from collapsing in the soft earth and keeps groundwater out while serving as short-term reservoir for overflows of drilling and fracing fluids. A rotary drill of up to 12 inches then begins to grind out a vertical well with tungsten carbide tips. Air is pumped down the drill stem to cool the bit and force cuttings to the surface.
The initial hole is drilled to a depth several hundred feet below any freshwater zones. (Most residential wells are less than 150 feet deep, while commercial and municipal wells are usable to about 400 feet.) A surface casing is then inserted in the bore hole, and concrete is pumped down to a shoe at the bottom which forces the concrete back up the annulus between the bore hole and the casing. This concrete-enclosed casing isolates the well from the potable aquifers and also keeps the groundwater and loose debris from contaminating the well.
A smaller bit drills through the concrete, continuing downward. Drilling mud, a high-density slurry, is pumped down the drill stem to cool the bit and force rock cuttings to the surface. So far, the process is identical to drilling a conventional gas or oil well.
But fracing gives a twist to the traditional process, literally. At about 500 to 600 feet above the shale formation of interest, at a point called the kickoff point (KOP) or heel, a “Measurement While Drilling” (MWD) motor is inserted in the bore hole and forces the bit off line. It traces an arc, entering the shale formation in a horizontal plane known as a lateral. The lateral continues on several thousand feet to the end of the shaft, known as the toe. Production casing is inserted and concreted in place, as was the surface casing. After pressure testing to several thousand pounds per square inch, the large drilling rig is disassembled, cleaned, and sent to another site where it will repeat the 10- to 14-day drilling process. The remaining work will be done by a smaller platform known as a workover rig.
To punch holes through the casing and concrete, and into the shale formation, a perf gun using multiple shaped charges is lowered and fired electrically. This operation, known as the wireline, begins at the toe and is done in increments of about 500 feet. Now the fun begins.
Fracing
If you’ve had the opportunity to drive a car made before 1930, you know how much force it takes to apply the brakes, given the lever-and-cable system used to force the brake shoe against the drum. The hydraulic brake allowed the automobile operator to do what seems quite anti-intuitive. By stepping on the pedal attached to a lever that pushes a plunger, hundreds of pounds per square inch of pressure are produced in the hydraulic cylinder containing brake fluid. As if by magic this pressure is conveyed to each of the wheel cylinders, thereby “applying the brakes” with little strain on the driver.
Hydraulic fracturing uses the same principle, though in this case the brake pedal is a group of large-capacity, high-pressure, diesel-powered pumps. The brake fluid is akin to one million gallons of water treated with certain chemicals and sufficient proppants — usually sand or spherical ceramic materials — used to prop open perforations formed in the shale by the perf gun and enlarged by hydraulic fracturing. The “brake cylinders” are the fissures in the shale where the pumps transfer tremendous pressure, widening the cracks so gas can flow into the production casing.
After one section is fraced, workers plug it so hydraulic pressure can be concentrated in the next section. The process begins at the toe and moves toward the heel. The last step is to remove all plugs so that the remaining fracing fluid flows out. Crews install a six-foot Christmas tree, as the valves and blow-out protectors are called, something of an icon to all the ingenuity and effort that has taken place more than a mile below the surface. The well is now ready to produce clean, abundant energy without which our civilization would soon slide back into the days of human hardship and misery, with lives that are short and brutal.
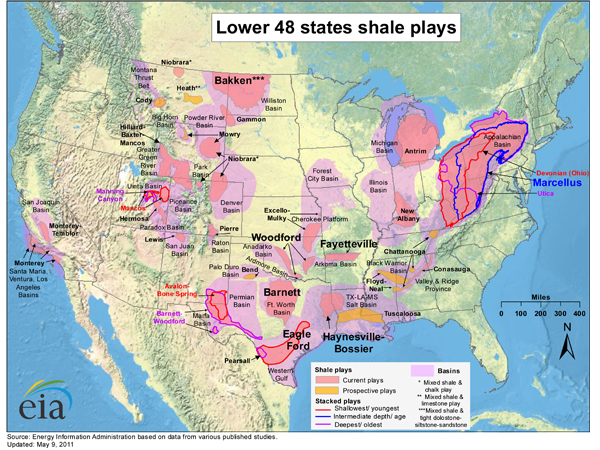
The Shale Gas “Plays”
You may have noticed that the natural-gas drilling and production industry has its share of special expressions, such as fracing, proppants, and wireline. Another word for what most of us would call fields (as in “oil fields”) is the play.
The first natural gas play was the Barnett Shale in north central Texas, where drilling began in 1981. Sixteen years of experimenting with the hydraulic fracturing process resulted in 404 minimally producing wells. As fracing was perfected and teamed with horizontal drilling in 2003, new wells were added by the thousands. Today, the Barnett Shale boasts about 13,000 producing wells.
The Bakken/Spanish/Three Forks Play located in Montana, North Dakota, and Saskatchewan (shown on the EIA map on page 12 as the Williston Basin) is currently the most active. Tiny Eagle Ford Play in south Texas along the Rio Grande runs a close second due to higher natural porosity than other formations. The huge Marcellus Play in the northeastern United States is third, but is a relatively untapped resource due to the unwillingness of the New York state government to allow its citizens to participate in selling what is unquestionably their property. Rounding out the top four is the Haynesville/Bossier/Cotton Valley Play in northwest Louisiana and east Texas.
Working in the Plays
The Fayetteville Play is a relatively small but active field supporting a booming shale industry in northern Arkansas. Andy and Brook Burton, co-owners of Trident Well Services, recently hosted TNA on a tour of several of its active drilling sites. Walking one of the sites, Andy Burton pointed out the 40 mil polyethylene sheet covering the active drilling area used to prevent any fluids leaking into the ground. It guides any spills or overflows to the cellar where they are contained until being pumped out and recycled. He noted the knee-high berms that keep liquids on the site in the event of accidental spills. Burton’s company is primarily responsible for ensuring that trucks and the drilling rig itself are cleaned before moving to a new location and that the site will meet the white glove test of the most rabid environmentalist when moved into the production phase.
The crews go about their 12-hour workdays with military precision. Regular interactive safety meetings, protective gear, and computer-controlled drilling that gives advance warning before high-pressure venting have lowered the accident rate until oil and gas field work is no longer considered a form of industrial suicide. “Three or four years ago the emphasis was entirely on production,” says Burton, “but today safety and environment concerns determine whether you maintain your MSA.” His reference is to the coveted Master Service Agreement necessary for eligibility to work for major companies such as Southwest Energy and Chesapeake.
The Future of Fracing
Today, the Natural Gas Association estimates that 90 percent of wells drilled today use fracing as a means to increase production. This technology has, in about four years, changed the natural-gas production outlook from what some feared to be a tailing off of production, to what is now known as the shale gale.
Research is under way into re-fracing natural-gas wells and developing even more efficient technology. One interesting new fracing method pioneered by Canada-based Gasfrac Energy Services, Inc. uses gelled propane instead of water as the fracing fluid. Under high pressure, the gel is liquefied and carries the proppants into the shale formation. When pressure is released, the liquid returns to its normal gaseous state. Gasfrac claims that virtually 100 percent of the propane is recovered and that 80 percent of truck traffic to the drilling site is therefore eliminated.
The primary argument by those opposing this ingenious way of bringing a valuable product from formations a mile underground to the surface for our use and comfort is that this activity will contaminate near-surface aquifers. Somehow fracing fluid (known from personal contact to be as bland as dishwater) is going to migrate through 4,000 or more feet of rock, sand, and shale into an aquifer. Or drillers would somehow allow the valuable product they are selling to escape from high-pressure concrete-encased steel casing into a water well. But the whole process is very environmentally friendly, and it’s getting even friendlier by the day.
Thumbnail photo of fracing operation: Cheesapeake Energy
Related article: